Variable flow of chilled water and condenser water is increasingly used to reduce pumping energy in chilled water systems. According to Bahnfleth and Peyer [19], the successful application of chilled water systems with variable primary flow depends on how the flow and chiller capacity can be adjusted to match changing load conditions. This application is specific rather than generic, and the airside cooling coils are required to be furnished with two-way control valves in order to allow the flow of chilled water to drop under the reduced load conditions. For a constant air volume (CAV) system where the latent load removal capacity is a concern, the potential of reducing chilled water flow rate under part load conditions is rather limited and so is the pump energy savings from this application chiller . Gordon et al. [20] highlighted that the condenser water flow rate could be a control variable in improving the energy performance of chiller systems. They established an analytic semi-empirical chiller model to study variations of chiller COP (coefficient of performance) at different condenser water flow rates. No analysis was made on the system level involving the interaction between the compressor power, pump power and tower fan power. The model serves well for fault detection and diagnosis purposes, but is incapable of accounting the control variables of cooling towers. No control regime was generalized on how the condenser water flow should be varied in response to various chiller load and wet-bulb conditions in order to achieve optimal energy performance of the system. Applying VSD to cooling tower fans can reduce their cycling frequency and allow better heat rejection control for any given chiller load while maintaining the cooling water temperature set point. This application constitutes a requirement for all tower fans with rated power exceeding 3.7 kW in ASHRAE Standard 90.1-2004 – energy standard for buildings except low-rise residential buildings [21]. Yet the true benefits of using variable speed tower fans hinge on how to control their speed to achieve system optimization. For conventional control of cooling water leaving temperature, a fixed and high set point of 3–4 C above the designed wet-bulb
temperature is often used to limit tower fan power, and hence the compressor needs to work at high condensing temperatures with a low chiller COP even when the chiller load or wet-bulb temperature drops. Some engineers tend to reduce the set point at the lowest possible level of around 15 C for all operating conditions to increase the chiller COP by minimizing the compressor power with more fan power. A fixed approach is an alternative method in which the set point is adjusted by a fixed value of 3–4 C above the changing wet-bulb temperature. This method assumes that the chiller load would change linearly with the wet-bulb temperature and that the tower fans can operate at lower speeds with power savings at the reduced wet-bulb temperatures. None of these temperature controls is a proven technique to achieve minimum energy use of chillers and cooling towers. Computer simulation is an expeditious means of analysing chiller system performance. Lots of chiller and cooling tower models have been developed in various forms. Pure empirical models generally fail to perform optimization studies as most control variables are absent. Transient models, on the other hand, are too complicated for general engineers to master easily and robust numerical methods are required to solve the differential equations. Moreover, they are cumbersome for carrying out hour-by-hour energy analysis of multiple-chiller systems frequently encountered. A general search for and comprehensive surveys [22,23] on many existing chiller and cooling tower models indicated that very few of them consider the interaction between chillers and cooling towers. Furthermore, none of individual models is capable of assessing power relationships of chillers, condenser water pumps and cooling towers together with water consumption in the heat rejection process, with regard to various control methods of cooling towers and condenser water pumps. Hydeman et al. [24] developed a modified DOE-2 regression-based chiller model for the variable condenser water flow application. One major task along with the model development was to ascertain which modelling approach would provide the most accurate simulation results with regard to the validation tests using manufacturer-supplied data and field-monitored data. Compared with other three public domain models – DOE-2 model [25], Gordon-Ng model [20] and ASHRAE Primary toolkit model [26], the modified model provided more accurate prediction over the chiller power, especially under low load conditions with variable condenser water flow or variable speed drives. The improvement in the accuracy of the modified model is due to the inclusion of the condenser water temperature along with the chiller part load ratio in the EIRFPLR function which expresses chiller efficiency under part load conditions. No control algorithm is included in the model to govern the cooling tower characteristics in terms of changes in the cooling water temperature under various airflow and water flow conditions for any given heat rejection. Lu et al. [27] presented a model-based optimization strategy for the condenser water loop of a chiller system. The strategy involved using a genetic algorithm to minimize the total power of the chillers, condenser water pumps and cooling tower fans. Regarding the physical constraints of the cooling towers, the interaction between the varying air flow rate and water flow rate for a given heat rejection rate was considered. The influence of condenser water entering temperature on both the chiller power consumption and cooling tower performance was considered. Yet they did not explain what set point should be used for the condenser water entering temperature to control the fan speed for optimizing the system. Benton et al. [28] developed a regression model to represent the improved cooling tower simulation algorithm (CTSA). No details were given about the mathematical expressions of the algorithm but the testing and comparison results were presented regarding the accuracy of the model against five CTSAs with the use of manufacturers’ performance data. The algorithm considered the cooling tower approach (cooling water leaving temperature subtracted from the wet-bulb temperature) as a dependent variable which is determined by the independent variables of the wet-bulb temperature, range (temperature difference of cooling water), condenser water flow and fan power. It remains uncertain how the algorithm can be used to evaluate an optimal set point for cooling water temperature as the cooling temperature leaving temperature is an implicit variable in the evaluation of cooling tower characteristics. Graves [29] reformulated the Gordon-Ng model in order to study more specifically the optimization of the whole system including two chiller-pump pairs and one cooling tower satisfying the nominal heat rejection capacity of the two chillers. To properly describe the chiller-tower interaction, a condenser load and condenser water leaving temperature was involved in the mathematical expression of the compressor power. The chiller model was coupled with a NTU-effectiveness model for evaluating the cooling tower performance. The modified model was capable of analysing how the system COP varied with the changing condenser water flow. Yet
the tower model discounted the water loss due to evaporation, and a single NTU value was assumed to represent the tower performance at different water and air flow rates ranging from 50% to 100% of their nominal levels. Two correlations were identified to facilitate near-optimal system operation: one is the linear relationship between the cooling water set point and the wet-bulb temperature (an analogy to the fixed approach method); another is the linear relationship between the tower fan speed and pump speed. It is worth promoting variable speed control as a standard environmental-friendly feature for condenser water pumps and cooling tower fans in water-cooled chiller systems and strengthening simulation techniques for optimizing such application. The aim of this paper is to assess the energy savings and cost benefits of applying optimal control to the cooling tower fans and condenser water pumps of typical water-cooled chiller systems. This paper first presents how a thermodynamic chiller model interacts with a cooling tower model to determine power relationships between the compressor, condenser water pump and tower fan under various operating conditions. The tower model, coupled with real control of cooling water temperature, is capable of simulating fan power and water loss by evaporation based on any given heat rejection and ambient condition. An assessment will be made on the extent of the increase in the system COP resulting from the optimum speed control of the tower fans and condenser water pumps. Discussion will be given on how the fan and pump speed can be controlled directly based on the chiller load in order to achieve optimum system performance. Following that, an example chiller system serving a local office building will be considered to characterize and compare annual electricity and water cost savings when applying various tower and pump control methods. The significance of this study rests on providing more quantitative analysis to promote water-cooled chiller systems with optimal operating schemes in order to boost their environmental performance in terms of annual electricity and water consumption, and, at the same time, to reduce their operating costs. 2. Description of the chiller and cooling tower models The chiller and cooling tower models were developed using TRNSYS 15 [30]. Fig. 1 gives the vapour compression cycle of the water-cooled centrifugal chiller studied. The saturated vapour refrigerant leaves the evaporator at point 1. From point 1 to point 10 superheating occurs when the refrigerant absorbs heat from the compressor motor. Point 2 indicates a pressure drop in the refrigerant entering the compressor when some of the refrigerant is throttled through the partially opened inlet guide vanes at part load. After the polytropic compression process the refrigerant at point 3 is desuperheated in the condenser to a saturated condition at point 30 . From point 30 the refrigerant is further condensed to the saturated liquid state at point 4. The saturated liquid refrigerant expands isentropically to point 5 before entering the evaporator. No pressure loss in the refrigerant pipelines was assumed, considering that changes in the condensing pressure and evaporating pressure due to the loss do not cause an apparent variation in the chiller COP. Given this, P1, P10 and P5 are equal to the evaporating pressure (Pev), and P3, P30 and P4 are equal to the condensing pressure (Pcd). Pcd Pev Pressure (kPa) Refrigerant specific enthalpy, h (kJ/kg) 1 2 Polytropic compression 1’ 3 4 3’ 5 Throttling of refrigerant at part load Fig. 1. Vapour compression cycle of the chiller. F.W. Yu, K.T. Chan / Applied Energy 85 (2008) 931–950 93
Each operating condition comprises seven inputs: dry bulb outdoor temperature (Tadb), wet-bulb outdoor temperature (Tawb), cooling capacity (Qcl), chilled water flow rate (mw), the temperature of supply chilled water (Tchws), condenser water flow rate (mcdw) and the temperature of cooling water leaving the cooling tower (Tctwl). The cooling capacity (Qcl), Tadb and the coincident Tawb would come from the hourly load profile of chillers operating for a given set of building cooling load and weather conditions. The chilled water flow rate (mw) was fixed at its designed level according to the interlocking operation of one chiller with one chilled water pump at constant speed. The temperature of supply chilled water (Tchws) was set to be 7 C in all operating conditions. The reset of Tchws for chiller performance improvements is beyond this study, considering that not all airside systems and chilled water distribution systems are compatible with this control. Unlike many past studies considering a fixed mcdw for all operating conditions, this analysis attempts to ascertain how mcdw should be varied to minimize the sum of the compressor power, pump power and tower fan power. There is no generic method to regulate mcdw under various operating conditions for optimum system performance. Based on the velocity limits of condenser water passing through the condenser, the acceptable range of varying mcdw would be 50–100% of the nominal flow rate. One trial in this study is to vary mcdw linearly with the chiller load in order to keep the temperature change of the condenser water roughly constant. This could enhance the stability of the cooling water temperature. The implementation of this control calls for the interlocking operation of each chiller with a variable speed condenser pump and a controller which regulates the pump speed as a function of the chiller load. The outputs or operating variables of the chiller were determined by the following sets of algebraic equations through an iterative procedure. 2.1. Evaporator model The cooling capacity (Qcl) of an evaporator is expressed by Eqs. (1)–(4): Qcl ¼ PLRQcr ð1Þ Qcl ¼ mwCpwðT chwr T chwsÞ ð2Þ Qcl ¼ mrqrf ð3Þ Qcl ¼ AUevLMTDev ð4Þ where qrf ¼ h1 h5 ð5Þ AUev ¼ 1 c1m0:8 w þ c2Q0:745 cl þ c3 ð6Þ LMTDev ¼ T chwr T chws lnððT chwr T evÞ=ðT chws T evÞÞ ð7Þ The method of log mean temperature difference (LMTD) was used to model the heat transfer performance of the shell-and-tube flooded type evaporator. The overall heat transfer coefficient of the evaporator (AUev) is described by a mechanistic relation in Eq. (6) [31], where c1, c2 and c3 are parameters to be evaluated based on the performance data of the chiller at full load and part load conditions. 2.2. Compressor model The chiller contained one refrigeration circuit and one hermetic centrifugal compressor within which inlet guide vanes were used to modulate the cooling output at between 25% and 100% of the rated full load capacity while controlling the temperature of supply chilled water at its set point. The volumetric flow rate of the refrigerant at the impeller outlet (Vr) can be evaluated from Eq. (8) [26,32]: V r ¼ Aimp Uimp tanðbÞ ni ni 1 P2v2 pðni1Þ=ni 1 U2 imp ð8Þ 936The states (enthalpy hadbl and moisture content xadbl) of air leaving the cooling tower were determined by Eqs. (33) and (34). Given xadbl, the mass flow rate of water leaving the cooling tower (mctwl) can be evaluated using the mass balance in Eq. (35), where the water loss rate due to evaporation is given by (mcdw mctwl). The cooling water leaving temperature (Tctwl) is related to the cooling water entering temperature (Tctwe) by Eq. (36). Tref is the water reference temperature and 0 C was used, hadbl ¼ hadbe þ eaðhawbl hadbeÞ ð33Þ xadbl ¼ xawbl þ ðxadbe xawblÞ expðNtuÞ ð34Þ mctwl ¼ mcdw maðxadbl xadbeÞ ð35Þ T ctwl ¼ mcdwCpwðT ctwe T refÞ Qcd mctwlCpw þ T ref ð36Þ According to the conventional approach to evaluating cooling tower performance, the heat rejection airflow rate (ma) is one of the inputs required to calculate the temperatures of cooling water, states of ambient air, etc. This is in contrary to the real situation where ma is a variable depending on how the tower fan is controlled by a set point of cooling water leaving temperature (Tctwl) or condenser water entering temperature (Tctwe). Where a constant speed fan is used, it will be cycled on and off to maintain Tctwl within the tolerable range of the set point. For a variable speed tower fan, the air mass flow rate varies by modulating the fan speed to satisfy the required Tctwl. Based on the aforementioned equations, an iteration procedure shown in Fig. 2 is required to solve ma based on a given Tctwl. For a given set of inputs (mcdw, Tctwl and Tawb) and Qcd computed by the condenser model, the range and approach of the cooling tower can be evaluated. Tctwl has to be set at above Tawb to achieve a positive approach (Tctwl Tawb) in order to calculate a logical heat rejection airflow rate (ma). The initial trial for the hypothetical wet-bulb temperature of air leaving the cooling tower (Tawbl) is taken to be the cooling water entering temperature (Tctwe) subtracted by 0.01 C. The fictitious specific heat Cpaf can then be determined, given the enthalpies and temperatures of the saturation air calculated at the leaving and entering conditions. The LMTD method is applied to describe the effective heat transfer coefficient (AUct) of the cooling tower, and ma is then computed by using the given relationship between Ntu and AUct. A new Tawbl can be calculated based on the ma computed and checked with its previous value. If the difference between the values of Tawbl in successive calculations is within ±0.005 C, then the convergent criterion of the solutions can be met and all other variables can be determined explicitly. Otherwise Tawbl needs to be deducted by 0.01 C in each iteration to repeat the calculation steps until the convergent criterion is satisfied. In cases where the computed ma is greater than its nominal level mar, mar should be used to determine the smallest approach and all other variables for the given set of inputs. The water evaporation rate of a cooling tower working under various operating conditions was computed according to the mass flow rate of air entering the cooling tower and the difference between the leaving and entering moisture contents of that air, i.e. ma (xadbl xadbe). The power of a constant speed fan (Ect) is the rated power Ectr multiplied by the factor (ma/mar), considering that the average cycling period of the fan during an hour is directly proportional to the required ma and assuming that the fan power increases as a linear function of the tower airflow. If the fan operates continuously at its full flow (mar) throughout an hour, the factor will be equal to one and its rated power will be taken up over that hour. While a variable speed fan is used, the fan law is applied and the factor becomes (ma/mar) 3 based on the fan law with the cube relationship between the power and flow rate. In this analysis, the variable speed drive was assumed to account for 3% of the power of the fan operating at any speed and the minimum flow rate delivered could be down to 10% of the rated flow rate. 2.6. Evaluation of operating variables The chiller and cooling tower models were used to evaluate all the operating variables based on any given input data and constant parameters. The flow charts in Fig. 3 show the relationships between the component models and how the operating variables were evaluated. The evaporator model started to compute PLR, Tchwr, AUev and LMTDev based on the inputs: cooling capacity (Qcl), chilled water flow rate (mw) and the F.W. Yu, K.T. Chan / Applied Energy 85 (2008) 931–950 939 temperature of supply chilled water (Tchws). It then calculated the evaporating temperature (Tev) and pressure (Pev), and refrigerant properties at the evaporator discharge (h1, v1). Given that the condensing temperature (Tcd) linked the compressor and condenser models, the operating variables of these models had to be computed altogether at a specific accuracy through an iterative procedure. The iterative procedure started with an initial condensing temperature (Tcdo) of 45 C in calculating the variables of the compressor model (the case: ITERo = 0). A degree of superheat (Tevsho) of, say, 3 C was initially assumed in order to compute the compressor power (Ecc). Iterations were carried out on each Tevsh calculated by the expansion valve model until Tevsh converged to within a specified tolerance of ±0.005 C. In the condenser model, the inputs consisted of cooling water leaving temperature (Tctwl), compressor power (Ecc), cooling capacity (Qcl) and the refrigerant mass flow rate (mr) satisfying the requirement of the Fig. 2. Procedure for evaluating the required air mass flow rate under the actual control of cooling tower fans. 94
the scheme 1 (the baseline). There is no significant difference in the trend of system COPs at part load with different wet-bulb temperatures when the set point of Tctwl is fixed at 29.4 C for all operating conditions. For a given wet-bulb temperature, the system COP is maximized at a part load ratio of 0.8–0.9, instead of at full load, and it drops considerably when the chiller load reduced from such part load ratios. This variation in the chiller COP is governed by compressor efficiency and the capacity control done by the inlet guide vanes. Comparisons were made on how the system COP varied under various tower fan and pump controls. As Fig. 6 illustrates, lowering Tctwl to 18.3 C could not bring an absolute increase in the system COP, though the compressor power was lowest for most operating conditions among the other operating schemes. Indeed, the system COP could drop by up to 10% when the chiller load reduced from a part load ratio of 0.8. This is because the tower fans operated at full speed continuously and the increase of the fan power exceeded the reduction of the compressor power. Except the 18.3 C Tctwl control, the system COP could be improved by reducing the condenser water flow rate via modulating the pump speed in response to the chiller load. This implies that keeping the temperature difference of the condenser water at the design level is a viable means to optimize the trade-off between the compressor power and condenser water pump power. The system COP could increase by various degrees for all operating conditions when using the 4 C approach or implementing the optimal Tctwl, regardless of whether the on/off or variable speed control was used for the tower fans and condenser water pumps. When the wet-bulb temperature was below 28 C, the percentage increase in the system COP was more noticeable at higher chiller loads when the 4 C approach control was in place of the 29.4 C Tctwl control. The system COP increased by 1.4–16.1% by using the optimum Tctwl and VSDs for both the fans and pumps. Such an increase tends to be significant at the minimum

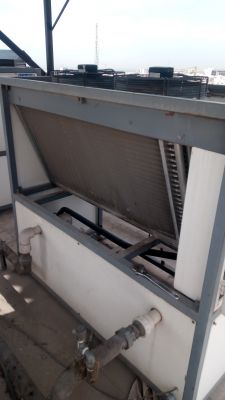